M.A. Ford Europe - a cut above.
This year’s MACH exhibition, back in April, was not only the most successful for M.A. Ford, since we first exhibited in 2014, but was also a key indicator of how far the company has developed during the past 10 years.
The introduction of new products, a growing technical sales and customer support team and a consistent programme of investment in our facilities at Derby and Leeds have all played a key part in the our success and represent three core strategic areas of - products, people and plant.
Products
Well known for a long history of product innovation, the development process has accelerated over the past five years with the introduction of new high performance solid carbide end mills and drills, together with indexable tooling including high feed milling cutters, drills and turning tools.
New ranges of thread mills, taps and specialised products, including the XFO oval form finishing tool and 5HC helical chamfer mills have also been added to the product line over the past 18 months, all of which are aimed at meeting manufacturer demands for increased productivity, tool life and versatility.
XFO Finishing tool
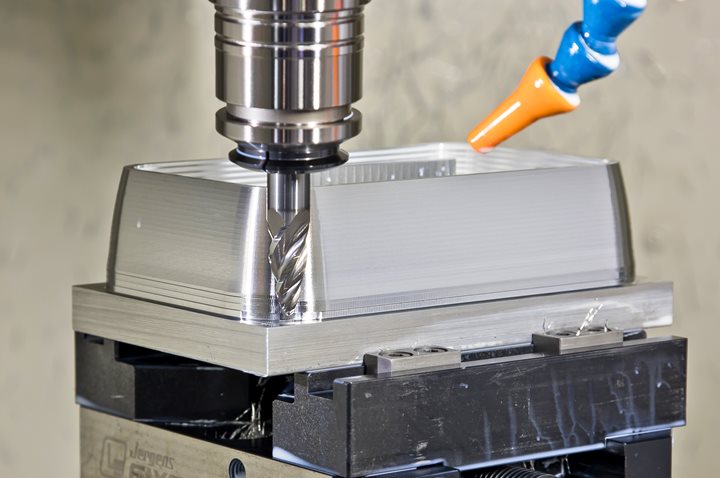
One of the most recent additions has been the TuffCut® XM series of micro-end mills, whose diameters range from just 0.1mm up to 6mm. Four separate products are included in the XM family, covering 2 and 4 flute designs, together with ball-nose, corner radius and square end options. All have a necked design for use on long reach and deep pocket applications, as well as 3D scanning and profile machining.
The launch of the XM Series coincided with M.A. Ford Europe’s appointment by Japanese high speed motor spindle manufacturer, Nakanishi, as a UK distributor and technical partner for their electric and air-turbine units, capable of spindle speeds up to 150,000 rev/min.
Designed to be mounted in CNC machine spindles, the Nakanishi units enable standard machining centres to be easily adapted and achieve the very high spindle speeds needed when using high performance precision tooling with small diameters, making them an ideal partner for the new XM Series.
People
Consistently exceeding sales targets over the last six years, stimulated partly by our move to larger premises in 2019, as well as increased manufacturing capacity, our team has also grown to ensure our high level of technical, sales and logistics support are maintained and enhanced.
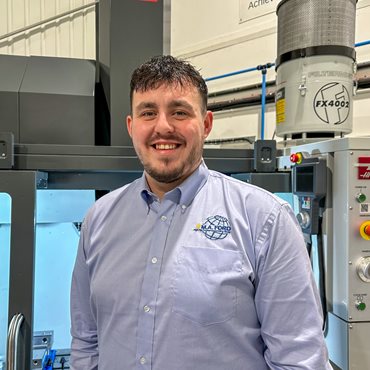
At our Derby HQ, new staff members in accounts, warehousing, sales order processing and administration departments, as well as a restructuring of the internal customer support team, has streamlined every aspect of order handling and customer servicing.
It’s a similar story at our Leeds manufacturing facility, where the arrival of new machinery has prompted recruitment in skilled staff, as well as the arrival of new apprentices.
Technical support is an essential area for the us and to reflect the sustained growth, we’ve taken on three new technical sales managers in the past six months, along with an internal technical support engineer, James Hayes - pictured right, who provides specialist product testing and support to the external sales team, distributors and end users.
Plant & investment
Ongoing investment in plant, machinery and manufacturing support facilities have been a feature of the business over the past decade with more than £7 million committed by 2019 including the creation of the new Derby HQ in the same year.
However, due to increased demand, a further £3.5 million was invested by the business during 2023 alone, which funded the expansion of UK production with advanced manufacturing machinery and an in-house coating plant.
Similar levels of investment have also been committed for 2024 with the installation of new CNC tool and cutter grinders, two centralised coolant systems and a doubling of the tool blank preparation cell capacity. Three Modula Lift automated vertical stock control systems (shown below) have also been installed at Derby and Leeds.